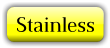
Stainless Steel Alloys |
13-8, 15-5, 17-4, 17-7, 301, 321 |
Sheet, Plate, Bar
You can send RFQs by filling out the RFQ form
below. Or you can
fax RFQs to 800-707-3439. We will get back to you ASAP.
* All Trademarks and/or Trade
names are the properties of their respective owners.
About Stainless Steel
Stainless steel is an alloy, which is iron-based and contains various
combinations of other elements to give it characteristics suitable for a wide
range of applications.
It is also called
corrosion-resistant steel or CRES, particularly in the aviation industry.
Most
stainless or heat resisting steels are either melted by the electric furnace
process or vacuum arc re-melted.
Heat
treatment for hardness and strength is recommended mainly for the straight
chromium steels. Cold working is generally utilized for the chromium-nickel
classes of steel and has the advantage of increasing strength while retaining
good ductility.
Stainless Steel:
13-8 Stainless Steel,
15-5 Stainless Steel,
17-4 Stainless Steel,
17-7 Stainless Steel,
301 Stainless Steel,
321 Stainless Steel
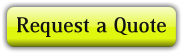
As your stainless steel supplier, we are capable of
fulfilling your required lengths and widths. California Metal & Supply Inc.
also has a stocking program to support long term contract for your stainless
steel needs.
13-8 PH:
13-8 is a precipitation, age hardenable stainless steel.
Stainless Steel 13-8's principal features
are high transverse toughness, good resistance to general and stress corrosion
cracking, and high strength that is developed by a single low temperature heat
treatment.
Applications
SS 13-8 has been used in aircraft components such as landing gear and
structural sections, valves, shafts, and components in the petrochemical and
nuclear industries.
15-5 PH:
15-5 PH is a chromium-nickel alloy containing a 5% copper additive, which
permits it to be hardened by low temperature heat treatments. The high
percentages of chromium and nickel give Stainless Steel 15-5 excellent corrosion resistance,
transverse toughness and forgeability.
Applications
SS
15-5 finds extensive use in the aircraft and missile industries for parts
ranging from instrumentation to landing gear components.
17-4 PH:
17-4 PH is one of the most widely used precipitation hardening grades in the business.
While soft and ductile in the solution annealed condition, Stainless Steel 17-4 is capable of high
properties with a single precipitation or aging treatment. Characterized by good
corrosion resistance, high harness, toughness and strength.
Applications
SS 17-4 is commonly used in both aircraft and gas turbines, nuclear reactor, paper mill,
oil field, and chemical process components.
17-7 PH:
17-7 PH is a precipitation hardening steel capable of reaching very high
strength and hardness without any loss of corrosion resistance. Surface scaling
and distortion in heat treatment is eliminated by Stainless Steel 17-7's ability to be treated at
very low temperatures. In the annealed condition, it has excellent ductility and machinability. It retains remarkable mechanical and physical properties at high
temperatures.
Applications
SS
17-7 is used for applications necessitating high strength, good corrosion
resistance and good mechanical properties at elevated temperatures.
Characteristic applications include surgical instruments, springs, bearings,
aircraft panels, and etc.
Stainless
Steel 301, 302, 304, 304L, 316/316L, 321, 410
301:
Stainless Steel 301 is an austenitic stainless steel manufactured by the electric furnace
process. Its chromium and nickel content are lower than most other grades,
offering the advantage of a high work-hardening rate which combines cold-worked
high strength with good ductility. Tensile strength and hardness increase
rapidly when Stainless Steel 301 is cold rolled, cold drawn, or worked at room temperature. The standards
of the aircraft industry are met by requiring adequate discard to be extracted
from each ingot.
Applications
Stainless Steel 301 finds its primary usage in products necessitating great strength, but
where working at elevated temperatures is not required. Used extensively in
aircraft components, truck components and bodies, decorative applications, and
etc.
302:
Stainless Steel 302 is an austenitic stainless steel. It provides useful
resistance to corrosion on a wide range of moderately oxidising to moderately
reducing environments.
Applications
Alloy 302 is used widely in equipment. Heat exchangers, piping, tanks and other
process equipment in contact with fresh water also utilise these alloys.
Building facades and other architectural and structural applications exposed to
non-marine atmospheres also heavily utilise the 302 alloys.
304, 304L:
Stainless
Steel 304
decreases the carbon content and thereby eliminates the possibility of intergranular corrosion. This low carbon alloy is most often utilized for
applications requiring welding. An Extra Low Carbon alloy, Type 304L is also
available for especially severe welding applications. Type 304L has the
capability to avert any detrimental precipitation in the extreme 800° F. to
1650° F. range.
Applications
Both types are extremely popular in the food and dairy industries and for use in
pharmaceutical equipment. It is exceedingly useful in applications where good
mechanical properties and corrosion resistance are essential. It is highly
desirable for products such as instrumentation where non-magnetism is
fundamental. These grades are available in a wide range of forms and finishes.
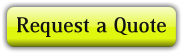
321:
Stainless Steel 321 is non-heat treatable and non-magnetic in the
annealed condition. This alloy contains 18% chromium, 8% nickel and a
substantial addition of titanium. The titanium forms insoluble and stable
carbide, which ties up all the carbon in the alloy and therefore prevents it
from precipitating as chromium carbides. This leaves the chromium in solution to
resist corrosion to a very high degree. This is extremely beneficial in high
temperatures, as it eliminates the necessity for re-annealing after fabrication.
Applications
Stainless Steel 321 is used principally for applications involving welding or sustained
elevated temperature operations where re-annealing is not practical, It is used
extensively in the aircraft and missile industries for engine parts, heat
exchangers, exhaust stacks, rocket engines, manifolds, and etc.
347: Stainless Steel 347 with its columbium
and tantalum content, is a stabilized stainless steel. 347 stainless steel has a
high resistance to prolonged heat and corrosion making it well suited for
engine, power generation, welded fabrications and other high heat applications.
347 stainless steel offers good mechanical properties with higher creep and
stress rupture characteristics than other grades.
Applications
347 stainless steel is widely used in aircraft exhaust, collector rings,
expansion joints and in high temperature chemical processing. 347 stainless
steel is also advantageous in applications that require omission of the
annealing process after welding.
410:
Stainless
Steel 410 is a
magnetic, martensitic, heat treatable alloy that is 12% straight chromium. It
has excellent creep strength and corrosion resistance. Heat treatments may be
applied to develop a very wide range of mechanical properties and hardness. It
is popularly used for parts operating at high temperatures.
Specifications
410 Stainless Steel: UNS S41000, Alloy 410, AMS 5613, ASTM A-276, ASTM A-314,
ASTM A-479, ASTM A-493, QQ-S-763
Applications
Because of its high strength and versatility in heat treatment applicability,
and because of its good mechanical and machining properties, Stainless Steel 410 finds
usage in a wide range of applications. It is used for low-cost cutlery, food
industry machine parts, pump shafts, valve parts, compressor shrouds, and
abrasive applications.
904L: Stainless Steel 904L is a low carbon high alloy
austenitic stainless steel, originally developed to resist corrosion in dilute
sulfuric acid. Because of the combination of relatively high contents of
chromium, nickel, molybdenum and copper, this grade has greatly improved
resistance to strong reducing acids, particularly sulfuric acid. Alloy 904L
tubing is non-magnetic in all conditions, possesses amazing toughness, and has
good formability and weldability.
Applications
Alloy 904L is found in many applications ranging from utility scrubber
assemblies, acid and fertilizer production equipment, pulp and paper processing,
seawater cooling facilities and many other uses.
316/316L: Stainless Steel 316/316L is
non-magnetic in the annealed condition and not hardenable by heat treatment.
316/316L is more resistant to atmospheric and general corrosive conditions than
any of the other standard stainless steels. The addition of molybdenum provides
an extra measure of corrosion resistance making this grade suitable for
applications involving severe corrosive conditions such as use in the chemical
industries and marine atmospheres. This grade of stainless may become slightly
magnetic when cold worked.
Specifications
316/316L stainless generally conforms to ASTM A240, ASTM A276, ASTM A479,
AMS 5648.
Applications
Alloy 316/316L is used extensively for equipment. 316/316L meets the exacting
standards of the aircraft industry. Widely used in the chemical industry. Used
for pumps and pump shafts, oil rig pumps and medical instruments.
HP 9-4-30: A high strength, low alloy steel.
Specifications
AMS 6526, UNS K91283
Applications
Alloy 9-4-30 Steel was conceived to be used in applications requiring high
fracture toughness in the 220/240 KSI tensile range. Typically used in aircraft
structural sections, this vacuum melted alloy exhibits exceptional cleanliness
and weldability.
Stainless Steel Sheet, Plate, Bar
& Tubing
1)
13-8 PH
Stainless Steel: AMS 5629, DMS 2100,
STM-05-602, STO160LB0013, ASTM-A564 (XM-13), AMS 5864, BMS7-322, RMS 150
2)
15-5 PH
Stainless Steel: AMS 5659, BMS 7-240, AMS 5862,
ASTM-A564 (XM-12)
3)
17-4 PH
Stainless Steel: AMS 5643, AMS 5604, AMS 5622, ASTM-A564
(TYPE 630), UNS S17400
4)
17-7 PH
Stainless Steel: AMS 5644, AMS 5528, AMS 5529, MIL-S-
25043, UNS S17700
5)
A286 Stainless Steel: AMS 5525, AMS 5726, AMS 5731, AMS 5732, AMS
5734, AMS 5737, AMS 5804, AMS 5805, AMS 5853, AMS 5858, AMS 5895, ASTM-A-453,
Gr 660 CL. B, PWA/LCS
6)
301 Stainless Steel: AMS 5517, AMS5518, AMS 5519, AMS
5901, 301 1/2 Hard Stainless Steel Per AMS 5518, 301 ANN: AMS
5515
7) 302 Stainless Steel: AMS 5516, AMS 5636, UNS
S30302
8) 303 SU Stainless Steel: AMS 5640 TYPE 1,
MIL-S-7720, ASTM-A582, AMS-S-7720, 303 Stainless Steel Round Bar x 12 FT
9) 303 SE Stainless Steel: AMS 5640 TYPE 2, AMS
5641, MIL-S-7720, ASTM-A582
10) 304 / 304L Stainless Steel: QQ-S-763, AMS 5639, AMS 5513,
ASTM-A240, 304 / 304L Stainless Steel Plate Per AMS 5511, 304 / 304L Corrosion & Heat Resistant Alloy, Cold Finished & Annealed Per ASTM-A580
11)
321 Stainless Steel: QQ-S-763, AMS 5645, AMS 5510,
ASTM-A240, 321 2D Finish Stainless Steel Sheet Per AMS 5510
12) 330 Stainless Steel: RA330, RA 330 UNS08330,
EN 1.4886, ASME-B536, ASME-B511, ASTM SB-563, ASTM SB-511, ASTM SB-535, ASTM-B535,
AMS 5592, AMS 5716, N08334, W88334, Seamless Pipe Sch 40
13) 347 Stainless Steel: 347 Stainless Steel Sheet, AMS 5512, UNS
S34700, UNS S34709, ASTM A 240, ASME SA 240, ASTM A262 Practice E, AMS 5646,
AMS 5680, ASTM A182, ASTM A276, ASTM A314, ASTM A473, ASTM A 269, ASTM A 479,
QQS 763, ASME SA182, EN10204 DIN3.1B, MSRR 5632, PWA 300, PWA F17 LCS, W.
Nr./EN 1.4550
14) 403/410 Stainless Steel: AMS 5612, AMS 5613, GE
B50A459B-S6, 410 Stainless Steel Welded Pipe
15) 440C Stainless Steel: QQ-S-763, AMS 5630, ASTM-A276
16) 450 Stainless Steel: GE B50A789A-S13
17) 904L Stainless Steel: UNS N08904, 904L Tubing, 904L Stainless Steel Tube Per
ASTM-A213, NACE MR0175
Alloy 904L tubing is a low carbon high alloy austenitic stainless steel, for
use in applications that require moderate to high corrosion resistance.
904L tubing is non-magnetic in all conditions, possesses amazing toughness,
and has good formability and weldability.
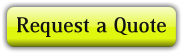
Types of stainless steel
There are different types of stainless steels: when nickel is added, for
instance, the austenite structure of iron is stabilized. This crystal
structure makes such steels virtually non-magnetic and less brittle at low
temperatures. For greater hardness and strength, more carbon is added. With
proper heat treatment, these steels are used for such things as razor blades,
cutlery, and tools.
Significant quantities of manganese have been used in many stainless steel
compositions. Manganese preserves an austenitic structure in the steel as does
nickel, but at a lower cost.
Stainless steels are also classified by their crystalline structure:
Austenitic Stainless Steel (Nitronic 50, Fermonic 50, XM-19), Austenitic (Nitronic 60), Ferritic, Martensitic, Precipitation-hardening
martensitic, Duplex
Austenitic or 300 series, stainless steels make up over 70% of total
stainless steel production.
Nitronic 50 Austenitic Stainless Steel
Nitronic 50 or Fermonic 50 Austentic Stainless
Steel is a nitrogen-strengthened austenitic
stainless steel that provides very good resistance to corrosion, abrasion and cavitation erosion, compared to alloys such as 316L and 317L. Even at low
temperatures it combines strength, ductility and toughness, so suiting it to
cryogenic components.
Specifications: Nitronic 50, Fermonic 50,
XM-19, Aquamet 22, UNS S20910
Fermonic 50 Annealed Alloy/ High Strength Grade/ Bar and Forgings: ASTM A479, S20910-XM-19
A, ASTM A276, S20910 XM-19 A, ASTM A182 F-XM-19
Applications: Chemical equipment,
especially processing sulphuric and nitric acids, fasteners, high-tensile
cables, down-hole tooling, exposed marine fittings, pulp and paper production
valves and fittings.
Characteristics:
Chemical Composition
FERMONIC 50 ingots are produced to a specified melting procedure using high
grade in-feed materials. Chemical analysis is carried out during analysis and
on the final poured metal.
Heat Treatment
Fermonic 50 Annealed Alloy Bar shall be delivered in a solution treated
condition. Solution treatment shall be carried out at a temperature above
1070˚ followed by water quenching.
Nitronic 60 Austenitic Stainless Steel
Nitronic 60 stainless steel alloy is an all
purpose metal that provides excellent high-temperature oxidation resistance
and low-temperature impact resistance. Nitronic 60, also considered a Super
Alloy, is designed to be the best non-galling stainless steel. Nitronic 60 is
a nitrogen strengthened austenitic stainless steel, with outstanding strength
and resistance to wear and galling. It has corrosion resistance better than
304, and pitting resistance better than 316.
Specifications: Alloy 218, UNS S21800, Cr
17, Mn 8, Ni 8.5, Si 4, N 0.13, C 0.10, Fe Bal.
Applications: Outstanding galling
resistance at both ambient and elevated temperatures makes Nitronic 60
stainless steel a valuable material for valve sterns, seats and trim;
fastening systems, including nuts and bolts; screening; chain-drive systems;
pins, bushings and roller bearings; and pump components such as wear rings and
lobes.
Characteristics:
Corrosion Properties
The corrosion resistance of NITRONIC 60 Stainless Steel falls between that of
types 304 and 316. However, experience shows that in a wear system, a galling
or siezure failure occurs first, followed by dimensional loss due to wear, and
finally corrosion. Galling and wear must be the first concerns of the design
engineer. Although the general corrosion resistance of NITRONIC 60 is not
quite as good as Type 316, it does offer better chloride pitting resistance,
stress corrosion cracking resistance and crevice corrosion resistance than
Type 316 in laboratory conditions. Corrosion tests are not normally performed
with NITRONIC 60 High Strength.
Corrosion Resistance
Nitronic 60 uniform corrosion resistance is better than 304 stainless in most
environments. The yield strength of Nitronic 60 is nearly twice that of 304
and 316 stainless steels. Chloride pitting resistance is superior to that of
type 316 stainless; Nitronic 60 provides excellent high temperature oxidation
resistance and low temperature impact.
Wear Resistance
This alloy provides a significant lower cost way to fight wear and galling
compared to Nickel or Cobalt based alloys.
Ferritic stainless steels generally have better engineering properties
than austenitic grades, but have reduced corrosion resistance, because of the
lower chromium and nickel content.
Martensitic stainless steels are not as corrosion-resistant as the
other two classes but are extremely strong and tough, as well as highly machinable, and can be hardened by heat treatment.
Precipitation-hardening martensitic stainless steels have corrosion
resistance comparable to austenitic varieties, but can be precipitation
hardened to even higher strengths than the other martensitic grades. The most
common is 17-4PH.
Duplex stainless steels have a mixed microstructure of austenite and
ferrite, the aim usually being to produce a 50/50 mix, although in commercial
alloys the ratio may be 40/60.
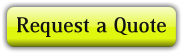
Zeron 100 Super Duplex Stainless Steel
Zeron 100 is a super duplex stainless steel for
use in aggressive environments. High strength, toughness, excellent corrosion
resistance in a wide range of organic and inorganic acids are just a few
characteristics that make this duplex stainless steel attractive to a variety
of industries. Lastly, it is highly resistant to strong alkalis and resists
corrosion in many non-oxidizing acids.
Stock Pipe & Fittings:
Zeron 100 Pipe Stock Size: Sch10 & Sch40 thru 12", Sch80 thru 6" Zeron
100 Fittings/Flanges: thru 8"
Specifications: UNS S32760, (J93380
Castings), Werkstoff 1.4501 (1.4508 Castings)
ASME: B16.5, B16.34, B16.47, B31.3, Sec. VIII Division 1 Case 2244-2,
2245-1, Sec. III Division 1 Case N-564-2
ASTM: A 182 (Grade F55), A 240, A 276, A 314, A 473, A 479, A 789, A
790, A 815, A890, A 928, A 988, A 995
Applications: Zeron 100, super duplex
stainless steel is used in oil and gas industry applications, pollution
control, pulp and paper, power generation, chemical, pharmaceutical, mining
and mineral industries, and marine industries.
2205 Super Duplex Stainless Steel
2205 is the most widely used duplex (ferritic/austenitic) stainless steel
grade. It finds applications due to both excellent corrosion resistance and
high strength.
Stock Pipe & Fittings:
2205 Pipe Stock Size: Sch10 & Sch40 thru 18", Sch80 thru 4" 2205
Fittings/Flanges: Available upon request
Specifications: UNS S31803, UNS S32205, Werkstoff 1.4462, EN 1.4462
ASTM: A 240, A 276, A 479, A 789, A 790, A 182 (Grade F51), A 923
ASME: SA-240, SA-479, SA-789, SA-790, SA-182 (Grade 51), ASME Pgroup 10H, NACE
ISO 15156 / MR0175
Applications: 2205, super duplex stainless steel is used in chemical
processing, transport and storage, oil and gas exploration and processing
equipment, marine and other high chloride environments, pulp and paper
digesters, liquor tanks and paper machines.
Ferralium 255 SD50 Super Duplex Stainless Steel
Ferralium 255 SD50 has been designed to harness
together the advantageous aspect of copper with the passivating elements
chromium and molybdenum in order to produce a superduplex stainless steel with
proven enhanced corrosion resistance in chemical and seawater environments.
Ferralium 255 SD50 is the preferred alloy for
large section forgings.
Specifications: UNS S32550, Alloy 255 High
Strength, F61
FERRALIUM to MSA-MPS-51VS-SD50-BAR, FERRALIUM to MSA-MPS-51VS-SD50-PLATE,
NORSOK MDS D57 Bar, NORSOK MDS D55 Plate, EN 10088-1 1.4507, ASTM A182 Grade
F61 UNS S32550 Forged Flanges, ASTM A240 UNS S32550 Sheet and Plate, ASTM A240
UNS S32520 Sheet and Plate, ASTM A479 UNS S32550 Bar, ASTM A276 UNS S32550
Condition A , ASME Approval as Table UHA 23 and Code Case 1883, NACE MR 01-75
Applications:
Ferralium 255 SD50 is used in chemical, marine/
oil & gas, civil engineering, pulp & paper and nuclear industries.
Characteristics:
All product forms of FERRALIUM 255-SD50 can be
easily welded, and this includes welding FERRALIUM to other stainless steels.
The solution heat treatment process for FERRALIUM 255-SD50 is carried out at
1070 Degrees C (+/-10 Degrees C) and this must be followed by a rapid quench,
preferably in water. FERRALIUM 255-SD50 alloy can be readily machined and it
has been found that its machinability is superior to other superduplex
stainless steels. Hot forming can be carried out between 1150 Degrees C and
1000 Degrees C.
Comparison of standardized steels
EN-standard
Steel no. k.h.s DIN |
EN-standard
Steel name |
SAE grade |
UNS |
|
|
440A |
S44002 |
1.4112 |
X90CrMoV18 |
440B |
S44003 |
1.4125 |
|
440C |
S44004 |
|
|
440F |
S44020 |
1.4016 |
X6Cr17 |
430 |
S43000 |
1.4408 |
G-X 6 CrNiMo 18-10 |
316 |
|
1.4512 |
X6CrTi12 |
409 |
S40900 |
|
|
410 |
S41000 |
1.4310 |
X10CrNi18-8 |
301 |
S30100 |
1.4318 |
X2CrNiN18-7 |
301LN |
N/A |
1.4307 |
X2CrNi18-9 |
304L |
S30403 |
1.4306 |
X2CrNi19-11 |
304L |
S30403 |
1.4311 |
X2CrNiN18-10 |
304LN |
S30453 |
1.4301 |
X5CrNi18-10 |
304 |
S30400 |
1.4948 |
X6CrNi18-11 |
304H |
S30409 |
1.4303 |
X5CrNi18-12 |
305 |
S30500 |
|
X5CrNi30-9 |
312 |
|
1.4541 |
X6CrNiTi18-10 |
321 |
S32100 |
1.4878 |
X12CrNiTi18-9 |
321H |
S32109 |
1.4404 |
X2CrNiMo17-12-2 |
316L |
S31603 |
1.4401 |
X5CrNiMo17-12-2 |
316 |
S31600 |
1.4406 |
X2CrNiMoN17-12-2 |
316LN |
S31653 |
1.4432 |
X2CrNiMo17-12-3 |
316L |
S31603 |
1.4435 |
X2CrNiMo18-14-3 |
316L |
S31603 |
1.4436 |
X3CrNiMo17-13-3 |
316 |
S31600 |
1.4571 |
X6CrNiMoTi17-12-2 |
316Ti |
S31635 |
1.4429 |
X2CrNiMoN17-13-3 |
316LN |
S31653 |
1.4438 |
X2CrNiMo18-15-4 |
317L |
S31703 |
1.4362 |
X2CrNi23-4 |
2304 |
S32304 |
1.4462 |
X2CrNiMoN22-5-3 |
2205 |
S31803/S32205 |
1.4539 |
X1NiCrMoCu25-20-5 |
904L |
N08904 |
1.4529 |
X1NiCrMoCuN25-20-7 |
1925hMo/6MO |
N08926 |
1.4547 |
X1CrNiMoCuN20-18-7 |
254SMO |
S31254 |
Please call 800-707-6061 or fax to 800-707-3439.
You can
click on the RFQ button below. We will get back to you ASAP. Thanks.
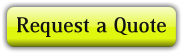